FABRIC
Fabric produced on a loom of two mutually perpendicular threads: the basics, running along the fabric andweftacross the fabric. The number of figures weaving weaves very large. The basic weave of the following:
simple or smooth (plain, twill, sateen, satin);
melkouzorchaty (matting, reinforced twill, diagonalise, Stardust);
complex (double, pile, openwork);
krupnozubchatye, or jacquard (a fabric with a large pattern in the form of patterns of flowers, etc.).
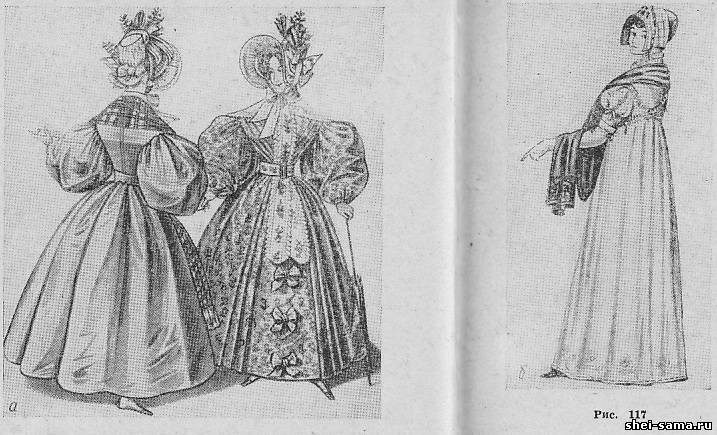
Between the dress and the fabric from which the clothes are made, have long been interrelated. So, in the SIXTEENTH and SEVENTEENTH and part of the EIGHTEENTH centuries produced a very dense, heavy fabric (cloth, velvet, camlet, brocade, etc.). They comply with complex and cumbersome costumes of those times. At the end of the EIGHTEENTH century the nature of women's costume changes dramatically, disappear frame heavy forms in Vogue are (due to the influence of ancient costume) clothing with soft fabrics (Fig. 117, a). Beautiful draping on a soft, light dyed fabrics, when every flapper gives a deep chiaroscuro.Of course, changes the texture (structure) of the tissue; appear muslin, muslin, muslin, cashmere is mainly light. In Vogue include percale (a cotton cloth) and linen.
By 30-th years of XIX century in the costume again begins to show the clarity of forms; to a slight change come tissues tougher, although less bulky and heavy than once (Fig. 117, b). This is moire, taffeta, REP, poplin, satin, kanaus, etc.
because each time a new characteristic lines, the silhouettes, the cut, the new technology, the result is often the emergence of new kinds of fabrics with new texture and processing properties, because the model a coat, suit or dress loses all its form if it is made of a bad or outdated, out of fashion fabric.
It should be noted that the raw material base of textile industry is very big. Particularly significant growth in recent years, the industry that produces various types of synthetic fibers - nylon, lavsan, Nitron. Tissue with a mixture of such fibers have good appearance, they have new valuable properties. Dacron, for example, resembles a natural wool fiber; moreover, he surpasses it in strength, no shrinkage, almost neminem, has the ability to retain creases, etc.
In the textile industry increasingly, the production of fabrics from mixtures of different fiber composition - wool with silk, wool with polyester staple fiber, silk cotton and synthetic fibers.
The extraordinary growth of the garment and textile industry leads to closer ties fashion designers and artists of the textile industry. This Commonwealth, on the one hand, contributes to the expansion and introduction of new kinds of fabrics (with new properties, pattern, color and quality), and on the other inspiring fashion designers in search of new forms of clothing.
A major role in the creation of a new range of fabrics played chemistry, greatly enrich and expand the existing range. Appear non-woven, film, dubbed, acetate materials.
Fabrics, designed for easy dress - soft, stretchy, drape well, good form any form (tunics, blouses, and lightweight summer coat, etc.).
For clothing widely used corduroy on foam, Plaksa corduroy (men's and women's jackets), rubberized nylon, etc.
Fabrics with lurex and metanotum intended for elegant dresses.
The variety of fabrics is not only the nature of the weave, color, pattern. The fabric is primarily different in its structure. The structure is determined by:
1) type and thickness of yarn;
2) the nature of the weave the yarn;
3) density.
From the structure and finishing of the fabric depend on its thickness, weight, mechanical properties, and a view of the front surface - texture.
The latter can be very diverse. There are fabrics with a smooth surface (e.g., fabric of satin and satin weaves), NAP (DRAP cloth), fabrics have a granular (crepe, pongee, boucle), tufted (beaver, velvet, polomarket corduroy, wale corduroy, corduroy) and others.
The tissue surface can be shiny, matte, rough, Krupenina, ribbed, ruffled, fluffy.
Some fabrics have elasticity and well-kept given them in processing form, others flaccid, friable, easily crushed, or, conversely, hard, dry, difficult.
So to imagine how the fabric is behaving in a particular case, it is necessary to test it on a dummy or figure and see if she is draped, soft or bristling in the tail and assemblies. Only after such verification, decide the suitability of a fabric for a particular model.
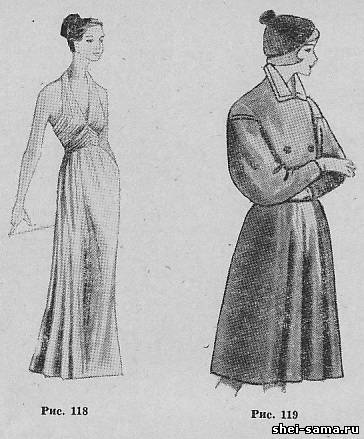
Dresses, suits and coats with soft lines, deep folds, drapery, accentuates the lines of the figure (Fig. 118, 119), should be manufactured from fabrics of the type Voile, crepe, Georgette, bouclé, Ratina, which have the ability to drape well.
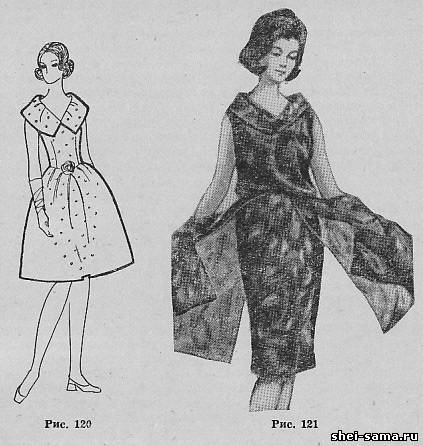
Fabrics for dresses and summer coats with wide, protruding skirts, tight fabrics, puffed sleeves and large collars (Fig. 120) should be hard, dense (such as taffeta, moire, reps, faille, poplin, pique, embossed satin).
Especially it is necessary.to say about transparent fabrics. These fabrics (of natural or synthetic fibers) can be soft and supple, elastic, hard and protruding.
The structure of such fabrics to diversify the use of various metallic yarn (lurex), as well as the production, reaching the ribbing, cheshuichatoe, satosti, corrugation, etc.
When deciding the composition of a particular model, given these General properties, inherent to transparent tissues, it is necessary first to reckon with the main feature - transparency. That is why the characteristic elements of the clothes are draping, Assembly, pleated, flying tunics (Fig. 121), ruffles; typical additions such as scarves, bows, capes, etc.
In models in sheer fabrics should not be a large number of stitches, patterns, lines, coquettes, as the latter in this case, the ugly are highlighted. Should not use hard creases, cover ~shirt fronts), collars, cuffs and pockets.
Compacted in these parts of the fabric (laid in two or three layers) becomes heavier, looks completely different than in the main parts.
Making the model transparent fabric, it is necessary to provide and cover. The fabric cover should be combined with the basic fabric and not to impoverish her. Moreover, it is necessary that the fabric cover facilitate the identification of the characteristics of the underlying tissue.
The texture of the ratio of the case and fabric of the dress are important elements in the correct solution of the composition.
Transparent fabric you can duplicate, sometimes with another cloth. This allows you to make seams nearly invisible, and the fabric is more interesting, the winning.
Physico-mechanical properties of tissues
Knowledge of physical and mechanical properties of tissues is important because in the process any tissue exposed to a variety of mechanical effects, stretching, shrinking, bending, friction.
The extensibility. Tissues characteristic of extensibility, and the warp threads they are stretched a little, on the weft thread much more, and in an oblique direction is particularly strong.
A number of tissues has the ability to greatly expand (faux crepe, crepe brands, pongee, sateen). Other fabrics (satin, corduroy, poplin, REP, taffeta, moire) are stretched a little.
The fabrics with high elongation, possible distortions. Unevenly stretched and sometimes separate items of clothing, especially in the oblique direction of the threads (coats in the middle of the back; the tails of the skirt flared in front, behind or on the sides, bodice with an oblique arrangement of filaments).
When grinding highly stretchable fabrics edges of the parts can stretch, the seam gets a wrong direction and spoil the whole look of the product. Most often it is manifested in the grinding of parts in oblique slices. Degree which the individual parts of these tissues may change their shape, the product will be distorted. Therefore, when developing a particular design associated with oblique sections, it is necessary to consider the ability of the fabric to stretch. In some cases it is necessary to make the brace parts cut, aligning and cutting at the same unevenness.
Products made of fabrics with great stretch and not subjected to special treatment (procrastination), ready to lose their shape.
Shrinkage. Property of a fabric to shrink, i.e. partially alter the length and width after the moisture and the wet-heat treatment, called shrinkage. Fabrics have different ability to shrink. So, cotton or silk pongee can give shrinkage of about 10÷12%, wool type fabric boucle is about 8÷10%, pure wool fabric type koverkot and gabardine - 3÷5%, staple fabric to 14%. Cotton plaid, wicker and satin almost do not shrink.
Shrinkage is useful and negative.
The shrinkage, which is inherent in pure wool fabrics, it is considered useful. The composition includes wool fibers of the cortical layer, contributing to the creation and long-term retention of a particular form achieved during the wet-heat treatment. Wool fabrics the s is different from other that their through wet-heat processing to stretch (brace) and cut (stojka) in some parts of the product (by the way, is what distinguishes the production of clothing out of wool fabric from the production of clothing fabrics cotton, linen, silk, synthetic fiber).
Formation of products from fabrics, not having the ability to cutivate well, much more difficult. In this case, the product has to give a certain shape exclusively design.
Under negative shrinkage mean total excessive reduction of the tissue under the action of water (rain, washing, cleaning) and wet-heat processing. Therefore, tissues having varying degrees of the ability to contract must be pre-processed - decamerone to stitched from these products during wear is not deformed.
Modeling any product, it is necessary to consider the ability of the fabric to shrink. Often obtaining the required shape is achieved by wet-heat treatment.
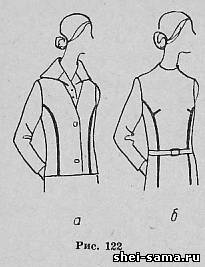
Here are two examples: the jacket straight from the fabric, giving the wet-heat treatment (Fig. 122 a), and the dress is straight of the fabric, not amenable to wet-heat treatment (Fig. 122, b). In the first case, the excess fabric in the seam Studeny, and the second - transferred to the dart.
Another example: if the fabric has a shrinkage, the flowing design of the sleeves reach through tuck in the top part of the sleeve (in the presence of the upper seam of the sleeve tuck combined with it).
Recently the textile industry has mastered the production of certain types of shrinkproofing woolen fabrics. Work is underway on the creation of non-shrink fabrics from other types of fibers (cotton, silk) and synthetic fibers.
Osypaemost. There are fabrics that have the ability to crumble the slices. This negative property. The highest flowability characteristic of worsted fabrics of coarse and polugrupa fur, fabrics, artificial silk and cotton fabrics.
In the simulation of articles of such fabrics should be avoided undercuts, complex reliefs, coquettes, and Welt pockets, wytycznych loops, gussets in cap sleeves. Otherwise, the fabric in these areas over time will spread, the product will lose its strength and appearance. In addition, it is necessary to increase the width of the seams are 1.5 - 2 times (in comparison with seams in products from tissues, is resistant to shedding) and their buttonhole. Hence, additional allowances for processing.
Tissue elasticity (creases).In the process of wearing fabric, non-elastic, easy to wrinkle. On different parts of clothes all wrinkly and samini why clothing loses its shape and form.
This property is determined by the elasticity of the fibres and fabric structure. Woolen fabric crumple a little, as wool is very elastic; linseed, on the other hand, quickly formed a deep samini and folds.
The denser the tissue and often the weave, the less the possibility of mutual shift of threads (warp and weft) bending of the fabric, the more elasticity and less creases.
The creasing of the fabric is one of the negative properties. If the fabric is very wrinkled, it cannot be used for too narrow, figure-hugging products, draperies, pleats, pleated. Such fabrics are not recommended for use in dresses, not cutting at the waist line, especially with a narrow skirt.
Splitting threads at the seams. This property is typical of fabrics made of natural silk and artificial fibres, wool and cotton fabrics (Voile, Shantung, reps, matting, pique,poplin,faille). When modeling the garment in the process of compositional development should avoid narrow forms. But in any case, grinding off parts seam to do wider, and the line more often.
Resistance to high temperatures. Tissues in different resistant to high temperatures. A number of fabrics, such as artificial fibers can not withstand the treatment with a hot iron: fabrics are sintered, change color, greatly reduced in length or width.
Pressing producing products, we must not forget that temperature is too high and too prolonged exposure to iron on the fabric lead to a weakening of the latter.
Special care should be taken when Ironing fabrics that contain artificial and synthetic fibers. Thus, non-observance of temperature modes in the process of Ironing rayon fabrics changes the color of the fabric, and sometimes strength decrease. TSNIISHP recommends Ironing these fabrics using damp cloth with the iron, the temperature of which does not exceed 160 - 180'C, not more than 30 C.
When ironed on viscose fabrics are often formed likvidiruet Lasy; therefore it is not recommended to prevent high pressure Ironing surface.
Dense, dry tissue sativus hard; the operation in this case, it is necessary to repeat.
|