The vehicles are part of the process of manufacturing products. The choice of vehicles depends from the configuration of production facilities and layout of workplaces in the stream; the length, speed and direction of the path (horizontal, vertical, inclined); the characteristics of the range, the process and system of organization of production and labor. Also take into account the safety and reliability of vehicles, efficiency and ease of maintenance.
In the garment industry used transport devices with mechanical or manual actuators and gravity, and the transporters with continuous and intermittent motion.
Vehicles driven include conveyors conveyors: belt and chain pendant.
Gravity, or besprovodnye, the device is majuscule, trays, rays, which are the subject of work manually pushing or dropping another artist.
For vehicles with manual transmission will carry a variety of trucks used for transfer of semi-finished product inside the shop.
The organizational forms of the production lines need to choose depending on the type of product, its design, applied technology, capacity, and power flow.
TSNIISHP recommends that in the design flow to apply the following vehicles.
I. For the manufacture of outerwear:
a) the workpiece parts (shelves, backs, etc.) - gravity transmission media (racks, ramps) with the batch run in a stream; a transport trolley or carriage-clips to the batch run in a thread; the mechanical conveyors with individually run to a stream (stream-average power);
b) mounting the sections - mechanical conveyors with a regular run in the stream; a gravity transmission media (racks, ramps) with the batch run in a thread (on the flows of large capacity, where the step of the conveyor does not meet a multiple of the transactions);
C) on finishing partitions - suspended conveyors regular run in the stream.
II. For the manufacture of underwear:
a) the workpiece parts (shelves, backs, etc.) - gravity transmission media (racks, ramps) with the batch run in a thread;
b) mounting the sections - gravitational means of transfer to the batch run in a thread;
C) finishing sections - suspended conveyors regular run in the stream.
III. For the production of needlepunched range (stream-high-power):
a) on the workpiece parts (shelves, backs, etc.) - gravity transmission media (racks, ramps) with the batch run in a thread;
b) mounting the sections - gravitational means of transfer to the batch run in a thread; the mechanical conveyors with individually run to the stream;
b) on finishing the sections - suspended conveyors regular run in the stream.
IV. For the production of needlepunched range (flux-small series): mechanical conveyors of the type TMS-1 and TMS-2 or gravity transmission media (racks, ramps) with the batch run in a thread.
Types of conveyors are distinguished by the number and arrangement of the transporting belts, the location of jobs relative to the bands and type of conveyor.
The conveyor serves to move the semifinished product between jobs. In the conveyor flow rate conveyor negotiates with tact, which contributes to the rhythmic flow.
Conveyor TMS-1 - bilinear, is designed to deliver boxes of parts and components to workstations and return the boxes with the processed parts to the launch site without the use of forced rhythm. At the end of the conveyor is rotatably mounted discs for transfer boxes parts with one conveyor belt to another. Rotary discs rotating synchronously with the tape. Both the conveyor belt located in a horizontal plane, the belt speed is constant 6 m/min.In the front part of the box arranged in the pocket for cardboard cards with numbers all manufacturing operations. Cards are arranged in accordance with the technological sequence of processing of products.
The use of conveyor TMS-1 has a number of advantages:
the possibility of a flow with mechanical transport of goods on a small production area - 100 - 120 m2;
conditions for the release of a large number of different products in small batches without rebuilding process;
maximum use of individual performance of workers independently of the cycle of flood and related operations by performing the worker several operations;
permanent securing of jobs and eliminate the need for the shifting of the equipment during the transition to new models of products;
at startup and removal of the finished product requires only one worker.
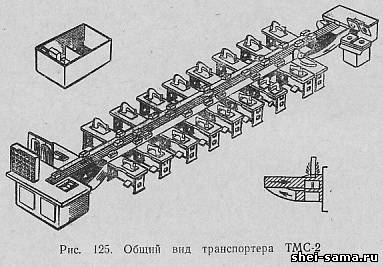
A disadvantage of TMS-1 are: increase of work in progress; the complexity of the account, carried out by means of account cards; additional area occupied two conveyor belts.
Conveyor TMS-2 (Fig. 125) - one-line, two-way layout of work places and adjoining ramps, designed to accommodate stock boxes. At the end of a conveyor device to automatically move boxes from the top branches of tape on the bottom, which moves in the opposite direction of flow and delivers the box to the table run. Lifting boxes on the table start-up is accomplished by means of the additional conveyor.
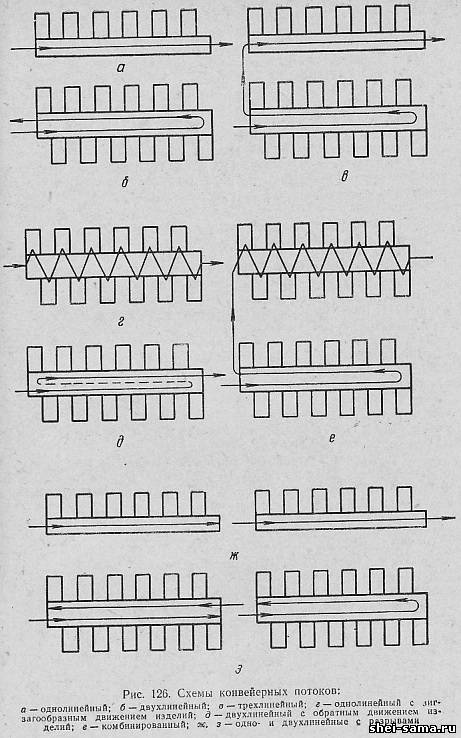
The use of TMS-2 compared with the TMS-1 has the following advantages:
the possibility of using the upper and lower branches for processing of products;
reduced area for conveyor installation on 50 - 60%;
reducing the number of drive and tension stations in 2 times;
decrease in the cost of manufacturing and installation of conveyor 4 - 5times;
reduce the cost of operation of the conveyor more than 2 times.
The drawback of installations of TMS-1 and TMS-2 is the lack of a device for automatic addressing of the boxes, i.e. offset them by the specified workstation.
On the mounting sections mnogofotonnykh sectional flow using various types of mechanical conveyors.
When moving articles to the main working places in the same direction, the process stream is called a single line, and the movement of goods in two or three directions, bilinear or trilinear.
The advantage of the single-row conveyor is that the launch and release of products is possible in different parts of the plant, but such conveyor should be applied in small editions (in the manufacture of linen, dresses, pants, etc.) in streams, the length of the lines does not exceed 40 - 50 m as the length of the lines complicates the work of staff.
The advantage of single-line double-row conveyor is a smaller footprint of the shop, but the drawback is the halving of in-process inventory of parts required for smooth operation, and a zigzag movement of the products to jobs (Fig. 126).
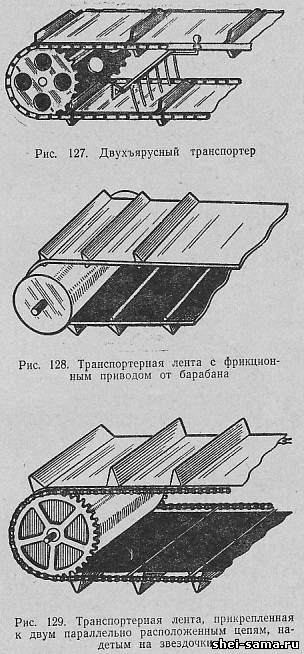
Bilinear and trilinear three-row two-row flows used in the manufacture of the upper, light clothing, linen, etc.
Most common in the industry got two-two-row conveyors with belt conveyor. Such conveyors, it is expedient to design the conveying passage between the belts for convenience and coaching of workers.
Conveyors can also be distinguished for the arrangement of conveyors: horizontal closed and vertical closed.
Horizontal closed conveyor used in the manufacture of products of small dimensions, as on the chain conveyor step cradles (the distance between their centers) is less than 0.4 m, the production area is used inefficiently.
Vertically-closed conveyor is widely used in industry as a basic type of conveyor.
For enterprises with small production shops used bunk belt conveyors on which partition to the cells do with the upper and lower sides of the tape (Fig. 127). Jobs come from both sides of the tape.
Pipeline flows are distinguished by the nature of the movement of products between operations and lines of treatment, which can be rectilinear and zigzag, depending on the number of rows of jobs and processing lines in the same conveyor stream.
Call rectilinear movement of products with the same number of rows of working areas and lines. If the number of series of jobs exceeds the number of processing lines, the movement of the products will be in a zigzag.
Between processing lines to transfer products is direct (normal) and reverse. Conveyor flows with the reverse movement of products between processing lines called conveyor flows with recirculation.
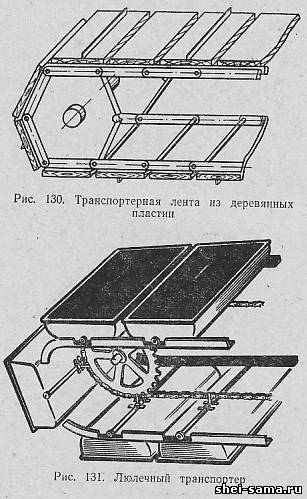
In the garment factories with the installation of conveyors used conveyors of various types:
1) the conveyer belt is divided into cells, the frictional drive from the drum (Fig. 128); this conveyor is the cheapest, but it does not provide constant speed movement of the products due to the sliding of the tape on reel;
2) the conveyer belt is attached to two parallel chains mounted on sprockets (Fig. 129); the tape is divided by partitions into the cell; this type of conveyor provides the projected speed of movement, as there is no slip tape on the drum;
3) the conveyer belt made of wooden plates are attached to two parallel chains,long links; thus the plate is divided by partitions forming the cells (Fig. 130);
4) chain vertically-closed conveyors with cradle cradles instead of cells; the cradle attached to the conveyor chains, hinged or rigidly; the movement of such conveyors is the chain transmission (Fig. 131), provides a specified rate; however, the production of cradles is laborious and requires expensive materials;
5) chain horizontally closed cradle conveyors with a chain, which is attached rigidly to the cradle; such conveyors require the accurate installation of the guides of the frame of the conveyor and fully provide the required speed of movement of the chain; 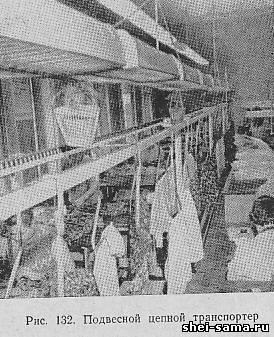
6) transporters of TMS-1 and TMS-2; they are made of cotton gummed tape; product is placed in special boxes made of sheet metal or laminated plastic;
7) overhead chain conveyors (Fig. 132); they are used to move finished garments in suspended form to better preserve the given shape in the last sections of the stream, where the final finishing and Ironing processing products; the products are hung on hangers in special holders (hooks) chain; overhead chain conveyor receives motion from the gear motor, and can be continuous or intermittent (pulsating) movement; in the absence of chain conveyors this section of the used mobile brackets that move manually.
|